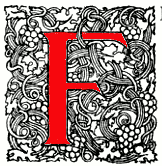
rom the earliest ages of the world the representation of natural objects by means of pictures, has been one means by which ideas have been communicated from mind to mind. The transition from pictures, which must necessarily be single objects, to engravings, by which the pictures might be multiplied extensively, seems natural enough—just, indeed, as printing from wooden or metal letters seems the regular and natural advance upon manuscript transcriptions. Thus, engraving may be considered as only another kind of printing—the design, executed on plates of copper, steel, or other substances, standing in the same relation to the picture as the metal types of the printer do to the caligraphy of the writer.
History of Copper Engraving
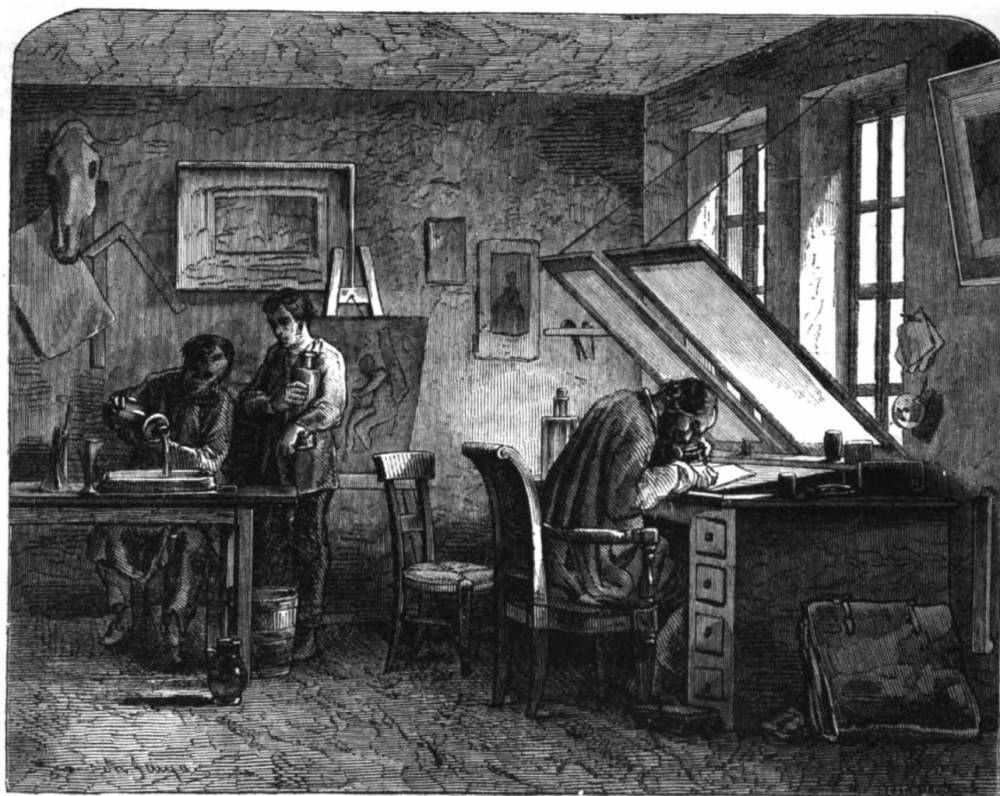
Figure 1. Engravers’ Workshop, — Engraving and ‘Biting In’
By the word engraving, we understand the art of executing designs upon copper or any other material, from which impressions or “prints” may be taken. It is usual to speak of its discovery as contemporaneous with that of printing, but in some sense the art was certainly known to the ancients; and our only wonder is, that so many years should have elapsed before its applicability to printing should have suggested itself. It is not, however, necessary to speak of the art of engraving as it was known to the ancients,— though we might refer, properly enough, to the writings of Moses for proof that engravings on seals and signets were known to the Egyptians; we might also speak of the numerous relics we possess in the British Museum of Etruscan, Grecian, and Roman art; and enter into a long description of the art of engraving on gems and metals, as it was known in India, China, and on the continent of Europe before the Christian era. But as our proper business is with the mechanical process of engraving on copper for the purposes of printing, we refrain from entering into these interesting particulars.
The invention of engraving, like that of printing, seems to have been the result of a kind of accident. Tradition attributes it to the Florentine goldsmiths of the fifteenth century. It is supposed that these artisans, or rather artists, while taking impressions of the subjects they had engraved, either on metal plates for the purpose of ornamenting furniture, or on gold and silver plate emblazoned by their hands, perceived that as the black, which remained at the bottom of the lincs, was readily taken off by clay or wax impressions, it might also be easily taken off upon paper. This first step was soon followed by a second, which was again quickly followed by others, and thus it was that the beautiful art was invented.
The invention of printing naturally gave engraving a new direction; and the engraver, hitherto a mere chaser and omamenter of metals for domestic uses, rose at once into the rank of teacher. The first prints were obtained from wood blocks engraved in relief. The earliest specimen of wood engraving known is one dated 1423, representing St. Christopher; but no impression from an engraved metal plate has been found of a date anterior to 1461. So that the art so common now has not yet celebrated its four hundredth birthday.
Tornmaso Fineguerra, a Florentine goldsmith, is said to have first practised the art of engraving on metal plates, for the purposes of printing, about the year 1460; but the credit of the invention has been of course claimed by others; the Germans — anxious sticklers for everything likely to advance the fame of their “faderland"—-put in their claim, but it is and had its origin in the workshops of the goldsmiths. Many of these goldsmiths were niellatori, or workers in niello — a mode of ornamental engraving usually performed on silver plates — the design engraved on which was afterwards filled in with a black composition.
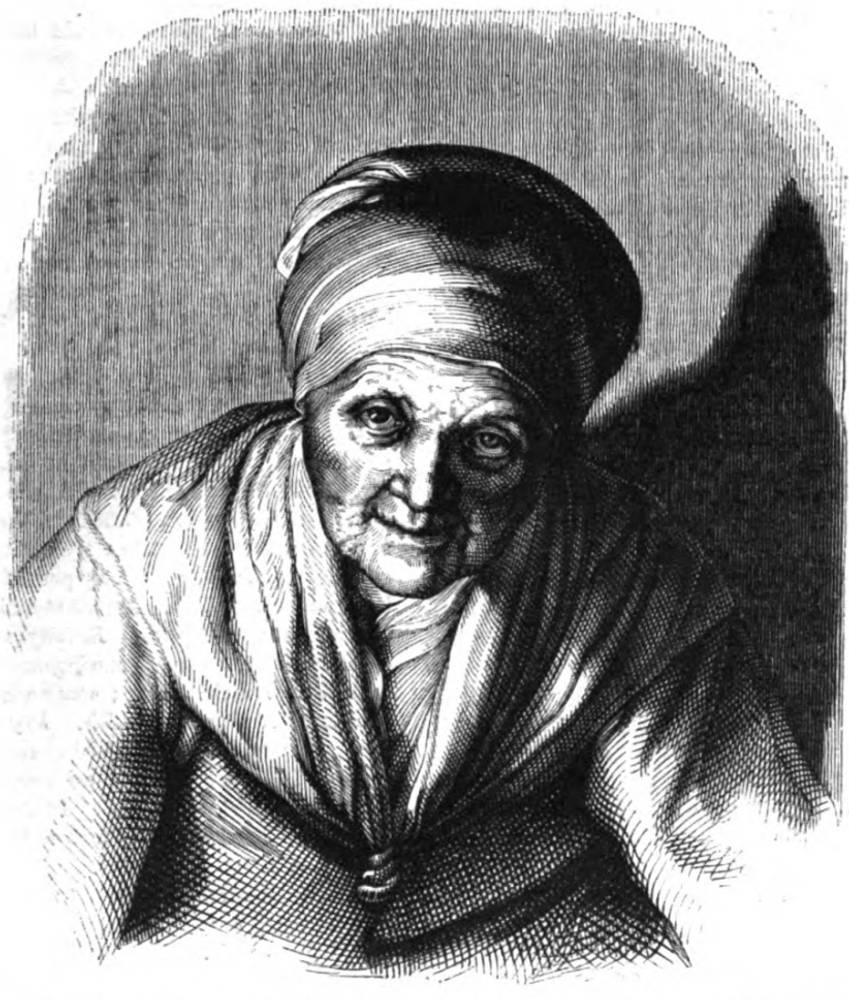
Figure 4. Fac-simile of a Copperplate Line Engraving, Produced on Wood.
This practice of his art naturally suggested to Fineguerra the possibility of taking an impression from the engraved design with ink on moistened paper. When once established, the new art was eagerly taken up by Baldini, Botticelli, Pollajuoli, and Mantegna; and in Germany by Martin Schoen, Israel van Mecheln, Leydenwurf, and Wolgemut. The first book printed at Rome -(an edition of Ptolemmus's Geography) was illustrated by the first plates engravings, twenty-seven in number, which were maps, and were executed there by two Germans, Sweynheym and Buckink. This work is dated 1478, but was commenced in 1472. Another early work was edition of Dante's “Inferno,” published at Florence is generally considered that the art was first practised in Italy, 1481, and embellished with engravings by Baccio Baldini, after the designs of Botticelli. One of the best engravers in Italy in the early part of the 16th century was Raimondi, who studied under Francia and Raffaelle. His great merit lay in the correctness and beauty of his outline. He engraved many of Rafaelle's pictures, which he copied with great truth, although defective in respect to light and shade. He was succeeded in Italy by Agostino de Musis, Marc de Ravenna, Caraglio, Giulio Bonasoni, and Enea Vico, all pupils of Raimondi; Georgi Ghisi of Mantua, and his relatives Diana and Adam Ghisi, Comelius Cort, &c. The principal painters who have practised engraving in Italy are Agostino Carracci, Stefano della Bella, Spagnoletto, Guercino, Salvator Rosa, Claude Lorraine, Swaneveldt, Canaletto, Piranesi, &c.
In Germany engraving made more rapid strides towards excellence, in the mechanical parts of it; and at the commencement of the 16th century appeared Albert Dürer, a man whose universality of talent extended the boundaries of every department of art, and carried all to a degree of perfection previously unknown in that country. He had great command of the graver, and carried his plates to a much higher degree of finish than his Italian contemporaries. He is also believed to have invented the art of etching by corrosion: three of his specimens are dated 1515, 1516, and 1518 respectively. On examining the etchings of Albert Dürer, we see that they have all been corroded at one “biting-in;” which sufliciently explains their monotonous appearance, and proves that “stopping out” was not then understood. The principal German engravers, after Albert Dürer, are Aldegraver, the Behmans, Altdorfer, Bink, Penz, Solis, &c.
Lucas Jacobs, best known by the name of Lucas van Leyden, was the father of the Dutch and Flemish schools, and the contemporary and friend of Albert Dürer. After Van Leyden the art was maintained in the Low (Countries by the Wierinxes, the Sadelers, whose works are multifarious, and embrace every class of subject; the elder and younger Jode, Cornelius, Theodore and Philip Galle, Abraham and Cornelius Bloemart, Goltzius, Sprangher, Müller, Lucas Killian, Matham, Saenredam, and the two brothers Bolswert. Many of these introduced improvements in the art. To mention the artists of this school from whose hands we have etchings, would be to name nearly all the most eminent painters belonging to it: Rembrandt, Berghem, Cuyp, Karel du Jardin, Paul Potter, Ruysdael, Ostade, Waterloo, Adrien Vandervelde, with many others.
In France engraving has been practised with pre-eminent success in the departments of history and portraiture. The celebrity of the school dates from the time of Louis XIV. The family of the Audrans produced six eminent engrsvers; but of those the most distinguished was Gerard Audran, who was the first engraver who successfully united, to any extent, the use of the graver and the etching point. Gerard Edelinck, although born at Antwerp, may be fairly considered of the French School, and was an engraver of the highest order. In portrait Nanteuil is no less celebrated than his contemporaries. The Drevets, John Louis Roulet, Le Clerc, Simoneau, Chereau, Cochin, Dupuis, Beauvais, Balechou, Le Bas, John George Wille, are among the best of the French engravers.
The English school of engraving dates only from about the middle of the eighteenth century, previous to which those who practised the art in England were chiefly foreigners. Hogarth engraved many of his own designs. Francis Vivares introduced the favourite art of landscape etching; he, Woollet, and Browne, produced some of the finest landscape engravings extant. Sir Robert Strange excelled in portrait engraving. Mezzo-tinto engraving, although not strictly born among us, has been in no other country practised with a degree of success at all approaching that attained by M‘Ardell, Earlom, Smith, Valentine Green, and others. Bartolozzi, Ryland, Sharpe, Paul Sandby, Middiman, Milton, Fitler, and Raimbach, are among the most eminent of deceased engravers (Knight's Cyclopedia of the Industry of all Nations).
The fifteenth and sixteenth centuries saw this art attain great perfection; this is incontestably proved by the chefs-d’oeuvre left by the old engravers; and the present and two preceding centuries have merely modified some of the old processes; though, doubtless, there are living at the present day some of the best and most artistic engravers the world has yet produced. It would be invidious to distinguish any by name; and our space would not allow us to give anything like a list of them and their works. The American school of engravers has yet to be formed; but the progress our artists are daily making leads us to hope great things of them.
Plates for Various Purposes
Copper, steel, zinc, or pewter plates, about the twelfth of an inch thick, are indifferently used for engraving upon. Steel is at present the metal most generally used, as the number of impressions which can be taken from it is very considerable. Copper is preferred for subjects of which fewer copies are required, zinc for plans or maps of very large dimensions, and pewter is the metal generally employed for music plates.
The Tools Employed in Copperplate Engraving
Copperplate engravings, such as are usually employed in the present day, are the result of two distinct processes; first, by direct incision of the graver, or of the dry point, and next by corrosion with aqua-fortis. The instrument called the graver or burin, differs in size, shape, &c., according to the character of the line which it is intended to produce, but the ordinary graver is of the form of a quadrangular prism, both square and lozenge-shaped, and fitted into a short handle, the whole being about five inches and a half long.
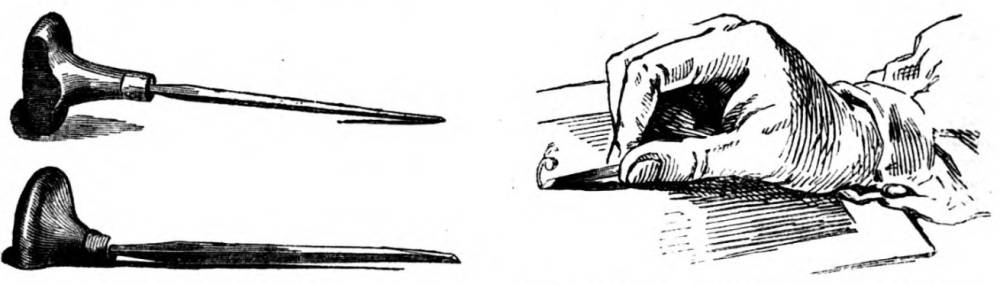
Left: Gravers, or Burins. Right: Way in Which a Line is Traced by the Graver..
The square graver is used in cutting broad lines, and the lozenge-shaped for more delicate ones. In making the incision it is pushed forward in the direction of the line required, being held by the handle at an angle very slightly inclined to the plane of the copper. It is requisite that the gravel be well tempered, and great address is necessary in whetting it for use. The angle at the meeting of the two lower sides of the graver forms what is called its belly, and the breadth of the end is called its face. The two sides which form the belly are to be laid flat upon the oil-stone, and rubbed firmly until the belly slightly rises, so that if it were laid flat upon the copper the light could be seen underneath the point; otherwise it would be impossible to use it with freedom, as it would dig unequally deep into the copper. The face is next to be whetted, which is done merely by laying the face of the graver flat upon the stone, with the belly upward, and rubbing it steadily upon a moderate slope until it acquires a very sharp point, taking care that the stone be properly supplied with oil all the while.
The gravers sold in the shops are commonly too hard for use, which is known by the frequent breaking of their points; when this is the case they should be tempered by holding them on a red-hot poker, at a distance of half an inch from the point, until they acquire a faint straw colour; they should then be put into oil to cool; or they may be tempered with a candle, and cooled in the tallow. But it is best not to be hasty in tempering; for if the graver is only a little too hard, whetting alone will frequently bring it into good condition.
An instrument called a scraper is required to scrape off the barb or burr which is formed by the action of the graver and dry point. The burnisher is used to polish the plate and to erase any scratches which it may accidentally receive, and also to make lighter any part of the work which may have been made too dark. An oil-stone is requisite for sharpening tho instruments upon. Etching-points or needles are nearly similar in appearance to sewing-needles, but fixed into handles four or five inches long; some are made of an oval form, to produce broader lines with.
Dry point is, in fact, nothing more than the common etching-needle brought to a very fine point. It is used to cut or scratch the more delicate lines with, such as skies, &c. &c. It does not, like the graver, cut the copper clean out, but throws it up on each side of the line produced by its progress through the metal: this is called the burr, which is removed by a scraper. This burr was left on by Rembrandt, until it wore away in the progress of printing, which it soon does; but by his management it added greatly to the effect of the etching, and impressions from his works with the burr on are much valued, A cushion is a bag of leather filled with sand; its use is to support the plate so that it may be freely turned in any required direction; but it is not now much used by artists, being chiefly confined to engravers of writing. A rubber is a roll of cloth tied up tight, one end being kept in olive oil. It is useful to polish off more completely the burr, and also to show the appearance of the work as it proceeds.
The Completion of the Engraving
Having thus explained the nature and uses of the tools employed in copperplate engraving, we shall soon briefly attempt to show how the engraving is brought to a state of completion. The outlines of the subject to be represented, with the form and place of the, lines which are to shade the engraving, are lightly traced on a steel or copper plate. Then a graver, corresponding in size and form to the lines required to be traced, is pushed forward, like a gouge, to cut the plate, by which means little strips of metal are scooped out. The strokes or lines, which are gradually increased in number near to one another, produce according to their position, their relative approximation, and their thickness, tints more or less varied, and the ensemble of the most perfect engraving is nothing but the ensemble of these strokes.
This process, which appears at first so extremely simple, is, however, excessively difficult to perform, and no one becomes master of it until he has served a long apprenticeship, and minutely studied all the mysterious difficulties of his profession. With respect to what is purely artistic, the acquirements necessary for one are also necessary for all kinds of engraving. The successful engraver must be an artist. There are some engravings which have only been terminated by the most assiduous labour of ten, twenty, or even thirty years. We even hear of a few plates which have each occupied nearly the entire life of an engraver.
Copperplate engraving is thus seen to be an assemblage of hollow strokes, forming a number of little furrows destined to receive the ink which is to be conveyed on to the paper, in order to produce an impression. Now, whether a plate has been engraved with the burin, or finished by corrosion with aqua-fortis, or by means of any other process, its surface always contains hollows for the reception of the ink which is to be convcyed, by means of the press, on to a sheet of paper ~—in this respect differing altogether from wood engraving, in which all that is cut away from the surface of the block appears white in the impression.
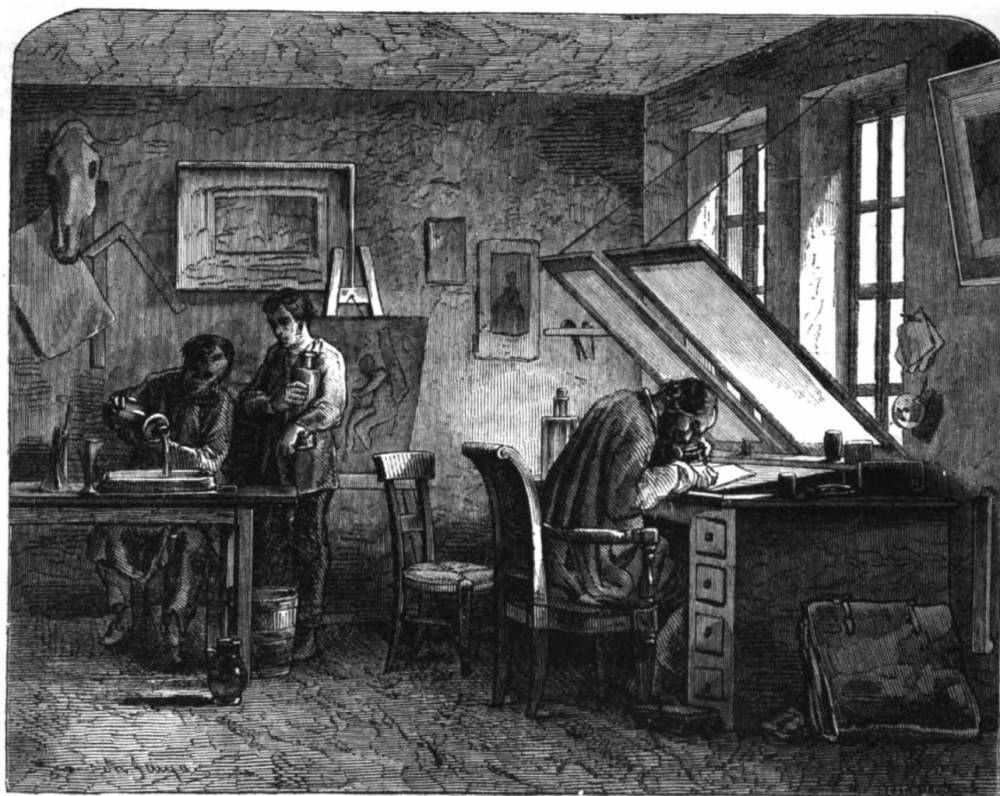
Engravers’ Workshop, — Engraving and ‘Biting In’
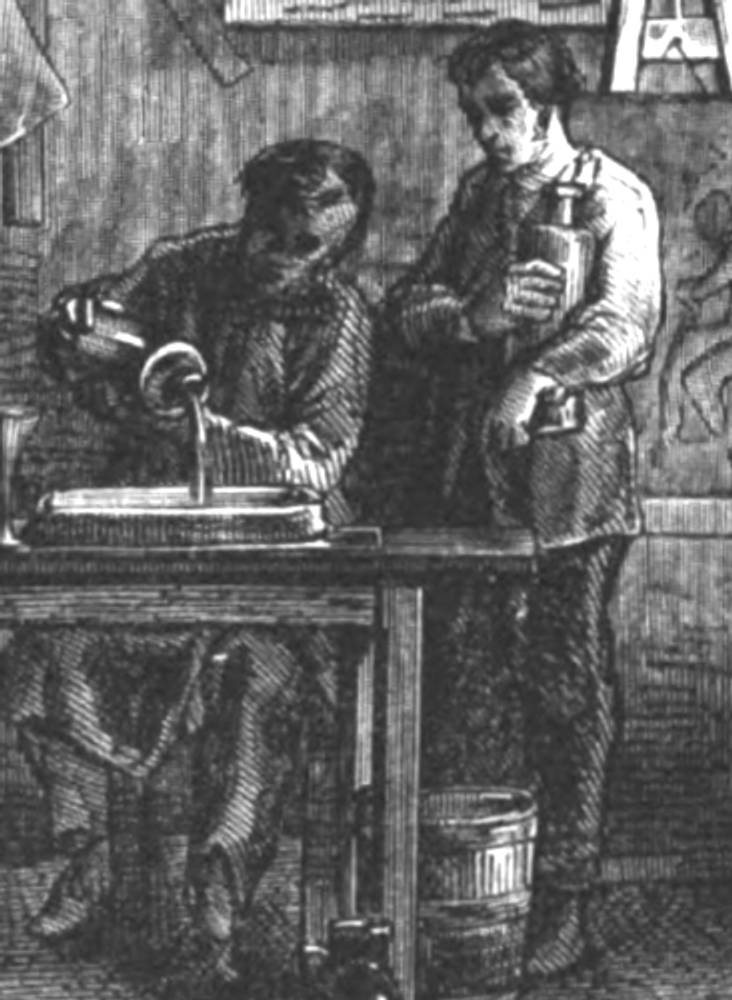
In the illustrations we have first, the workshop of the engravers (fig. 1.) which gives a pretty good idea of the general appearance of such an apartment, and shows how the various operations are carried forward; the artist himself working on the plate by means of reflected light and a powerful eye-glass, and his assistants engaged in the operation of “biting in" with aqua-fortis or other corrosive acid, an operation common to nearly all modern engravings; — secondly, a representation of a pair of gravcrs (fig. 2), which differ from those used in wood engraving only in being rather smaller, and of harder metal; — thirdly, the method of using the graver or burin (fig. 3);— and fourthly, a fax-simile of an engraving produced entirely by the burin without corrosion (fig. 4). In this last illustration we have an excellent example of engraving on wood,-—-the cross lines, shading, and general effect of awork on copper being admirably rendered. Indeed, so extremely diflicult is it to produce this kind of work in wood, that not more than half a dozen artists in London would imdcrtakc to produce a duplicate of our little picture, any one of which half-dozen would require to be paid about £5 for the task.
Copperplate Printing
We now come to the next stage of the operation — the print ing from the copper or steel plates thus engraved on. The design being “proved,” that is, impressions being taken from it to show that it is sufficiently well engraved to “go to press,” the plate is inked over, and then passed between the cylinders of the press, by which means all the ink upon the plate is transferred to the wetted paper laid upon it.
The mechanism of a press is very simple, and yet few persons have a true idea ofit. It consists simply of two cylinders or rollers, supported in a strong wooden frame. The cylinders are moveable on their axes, one being placed just above, and the other just below, the level of the table on which the plate to be printed is laid. The upper cylinder is turned round by the arms of a cross fixed to its axis; though in some of the more modern coppcrplate presses, a lever of greater power is employed. Our engraving will give a good idea of the form of this very simple kind of press; but it must be stated that the rollers may be brought closer or otherwise to each other according to the amount of impression; or rather, the depth of blackness required in the engraving.
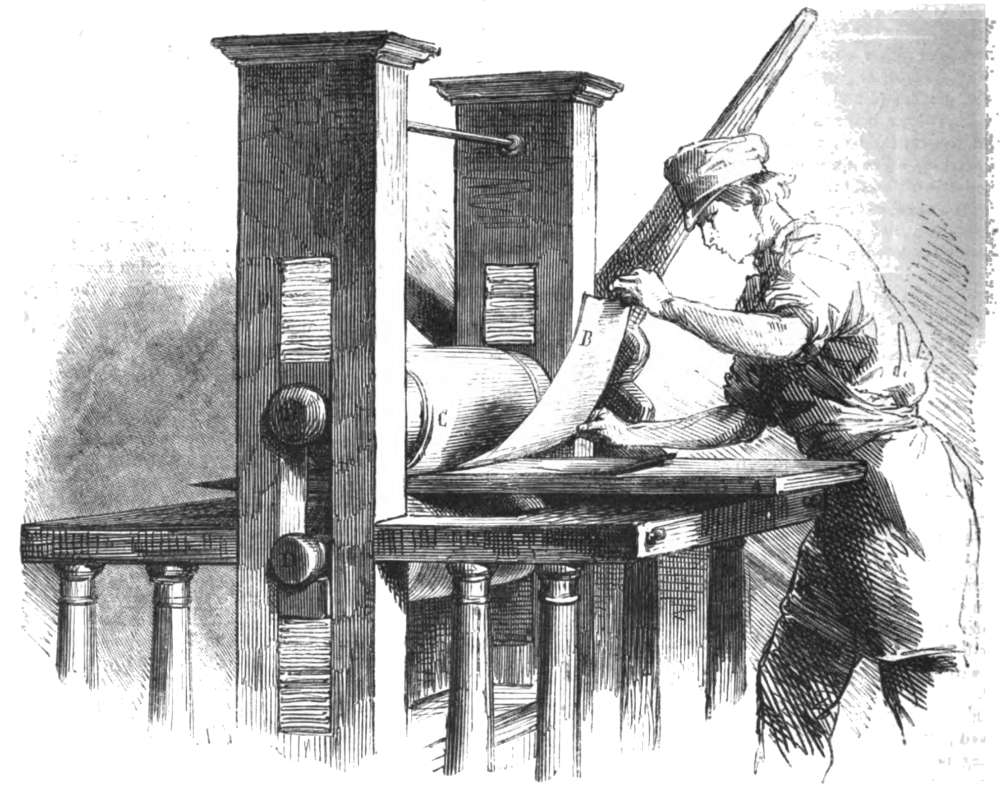
Figure 7. The Copperplate Press. — Taking the impression from the plate.
In the illustration (fig. 7), A, represents the board or table on which the engraved plate is laid; B, the sheet of paper about to receive the impression from the plato beneath; C, the upper cylinder with the blankets attached, and D D, the axes of both rollers. The means taken to move the cylinders higher or lower are very simple, being nothing more than the insertion of pieces of card-board into the longitudinal slits in the framing of the press, which cards act as a kind of slight spring during the action of the cylinders upon the plate between them.
The plate, then, has first to be inked. The printer to whom it is confided places it on a sort of box, the top of which consists of a plate of sheet-iron, and in which is placed a pan filled with lighted charcoal dust (fig. 5). When the plate has attained a certain degree of gentle heat, the printer removes it from the charcoal box, and covers it as equally as possible, by means of a dauber, with a light layer of brayed black, or copperplate ink (fig, 6),
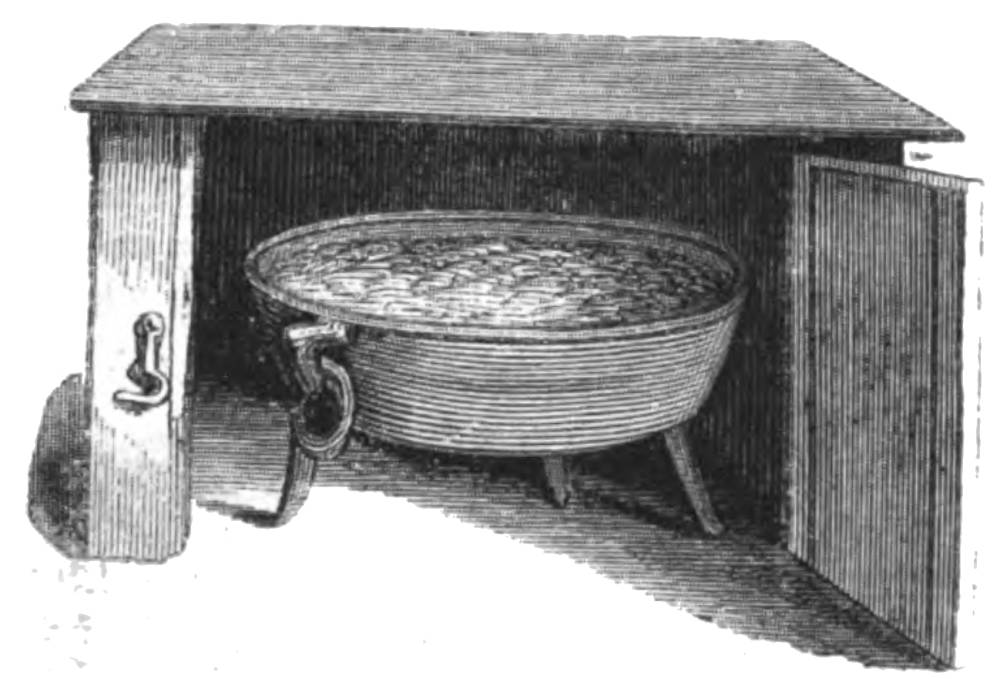
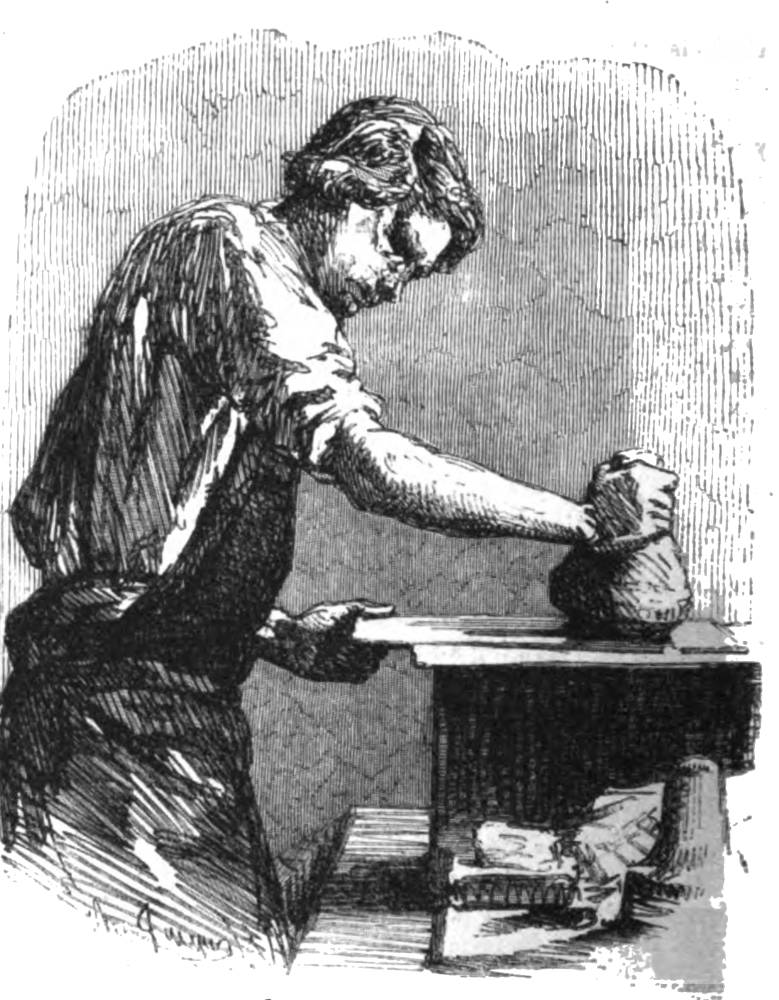
Figure 5. Left: Charcoal pan, or “Brazer”.Figure 6. Right: Inking the Plate. [Click on images to enlarge them.]
Inking the plate is an operation requiring great care and no small degree of skill, as, if too much or too little ink be employed, tho impression is greatly injured, if not entirely destroyed. Among copperplate-printers this kind of ink is technically called “black.” It is composed of very thick boiled oil, mixed with a proper quantity of Frankfort charcoal, produced from vine twigs. Of course, there are many varieties of copperplate ink, and many printers prefer to prepare their own.
This “black,” being slightly liquified by heat, enters the most superficial cuts on the plate. A piece of coarse muslin is then taken by the printer, and, by rubbing it on the engraving, the black is made to enter all the lines, while the superfluous colour is, at the same time, removed from the surface of the copper, which is polished bright by similar means. The printer, lastly, uses the palm of his hand to wipe off what ever black remains on the surface of the plate. This is a very delicate, though not a very clean, operation; a clever workman leaving all the lines of the engraving filled with ink, while the plain parts, which are intended to appear white in the impression, are made bright and smooth by the manipulation of his hand, assisted by a little whiting.
The engraving is now placed on a large walnut-tree board, (fig. 7), where it is covered with a sheet of damped paper, B, and four or five pieces of blanket, the texture of which is something between flannel and cloth, C, are placed on the sheet of paper. -These blankets are of course fixed to the upper cylinder of the press.
The plate, paper, and blankets are then passed between the rollers of the press. The workman, taking one of the arms of the cross in his hands, fixes his foot against the frame of the press, and by dint of sheer bodily exertion forces the whole through the cylinders, and thus produces the impression required.
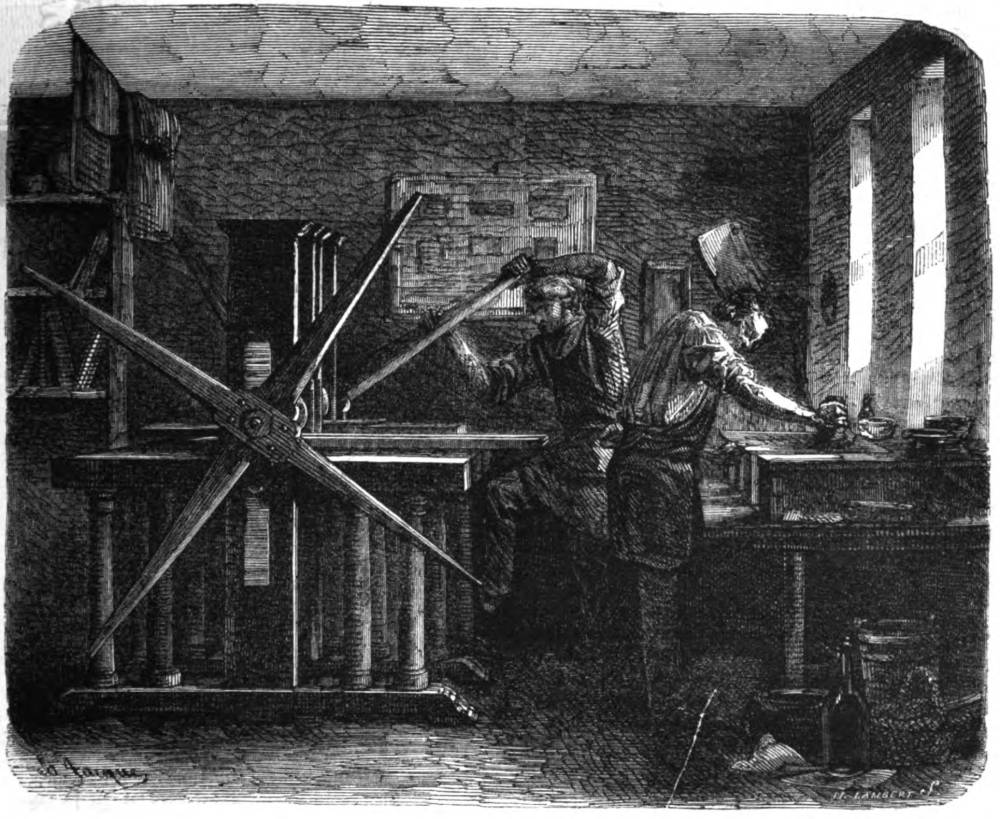
Figure 8. The Press Room. — “inking” and “pulling” the plate.
The rollers, or cylinders, are composed of walnut wood, lignum vitae, or steel; and as they are very close together, the leverage exercises enormous pressure. Indeed the philosophy of the process is simply that the pressure employed acts upon the elasticity of the cloth, and forces the moist paper to enter the lines in the plate and to take up all the black ink from it.
The proof is then removed from the plate; and this quick and wonderful operation, which can bo repeated as often as required, presents us with the innumerable impressions which ornament our books, our houses, and some few of our public galleries.
We have most of us heard of “artists’ proofs,” “proofs before letters,” “India paper proofs,” and “early copies” of engravings, many of which are sold for large sums of money; but not many non-professiorml readers quite understand the meaning of the several terms. We will enlighten them. “Artists’ proofs,” then, are some few, taken with peculiar care, — under the immediate inspection of the artist himself, — upon India paper; they are the first impressions of the completed engraving, and are sold with the autograph of the Painter or engraver attached, as a guarantee of their value. “Proofs before letters" are impressions carefully taken on India paper, immediately after the artists’ proofs, at the ordinary press, and before the plate has had the inscription attached to it by the writing engraver. “India paper proofs" are simply copies printed on India, instead of the usual unsized cartridge paper; and “early copies" are what their name imports—though all these terms are liable to great abuse. The India paper is accurately laid on the wetted sheet of cart ridge, and both together being passed through the press, the pressure exerted is suflicient to attach them inseparably together, the dampness of the cartridge slightly softening the size finish of the India paper. As a proof that nothing should be wasted, it may be mentioned that the fine tissue-like paper so much valued, is made from old ships’ ropes and tarred cordage!
Brief Notice of the Etching Process
As we shall have to speak more fully on another occasion of the aqua-fortis process, we conclude our notice with a brief account of the manner in which what is called etching is performed. As most persons know, and as we have before stated, etching is the super-addition of the “chemical process to drawing, when performed on a plate of copper over which a substance called the etching-ground’ is laid” (Penny Cyclopaedia). This etching ground is composed of wax, asphaltum, gum mastic, resin, etc., incorporated by melting over a fire, and capable of resisting the action of aqua-fortis. The laying of the ground, as it is called, is thus effected: — The plate must be heated over a charcoal fire, so that it may not be smoked. For this purpose a hand-vice is fixed to the most convenient part of the plate, by which it may be held in the hand. A piece of the etching ground, rolled into the form of a ball, and tied up in a little silk bag, is then rubbed over the surface of the plate, the heat of which causes the ground to melt and come through the silk on to the copper. In order to effect a more equal distribution of the wax, a small dabber made of cotton wool, tied up in a piece of taffety, is quickly dabbed all over the face of the plate while yet warm, so as to leave the wax or etching-ground of uniform thickness; the ground is then rendered black by being held over the smoke of a wax candle, or, if necessary, two or three wax candles tied together, care being taken to move the plate about, so that it be equally smoked all over; and this operation of smoking must be com menced before the plate has had time to cool. The whole operation of laying the ground requires address and dexterity. When cold, the plate is now ready to receive the design. To transfer the design to the copper, an outline is made with a black-lead pencil on a piece of thinnish and even paper, and laid with the face downwards on the etching-ground; the whole is then passed through a rolling-press, the eflect of which is to transfer an impression of the outline on to the smoked groimd. After this the design is completed with the etching needles, which remove the ground from the copper wherever they pass, and expose it to the action of the acid during the process of biting in, which is thus performed: — A substance called banking wax, which when cold is quite hard, but which on immersion in warm water becomes soft, and may be moulded into any form, is first rendered soft by being so immersed in warm water, and then banked up all round the margin of the plate, so as to form a trough capable of preventing the escape of the acid, s gutter only being formed at one corner for the purpose of pouring it off when requisite. This being done; the nitrous acid, reduced with water to the proper strength, is poured on, and its action on the copper becomes visible by the rising of innumerable bubbles. The aqua-fortis must be allowed to continue on the plate until the fainter parts are supposed to be corroded suffi ciently deep; after which it is to be poured off, the plate washed with water, and left to dry. The parts which are bitten-in enough are now to be covered with what is called stopping-ground, which is a mixture of lamp-black and Venice turpentine; this is applied with a camel-hair pencil, and allowed to dry. After this the acid is again poured on, and this process of stopping-out and biting-in is repeated until even the darkest parts are sufiiciently corroded. After this the plate is again warmed, when the border of wax may be readily taken off. It is then made warm enough to melt the ground, which is removed by being wiped with a rag and a few drops of olive oil. The work is now complete, unless it is intended to finish it still further with the graver. We might here offer rules for the strength of the acid, and state the length of time it ought to remain on the plate, but we are convinced of the inefficacy of such instructions. Nothing but experience joined to some chemical knowledge of the effect of the acid will avail the artist on this point, which requires the greatest nicety and attention.
Bibliography
“Engraving and Printing on Copper.” The Illustrated Magazine of Art. 1 (1853): 292-97. Hathi Trust online version of a copy in the Princeton University Library. Web. 28 December 2020.
Last modified 1 January 2021